Störungen vermeiden, ohne unnötig zu warten: Das ist die Königsdisziplin der Instandhaltung. Vielversprechend sind zustandsbasierte Wartungsstrategien für die etablierten Systeme mit KI-basierten Modulen kombiniert werden.
Bild zVg von PSI
Unerwartete Störungen des Produktionsflusses kosten Geld. Denn mit einer geringeren Auslastung sinkt die Overall Equipment Effectiveness (OEE), während die Produktionskosten steigen. Diese Gleichung gilt seit den Anfängen der Produktion. Die Lösung in der Vergangenheit: vorbeugend und in regelmässigen Zyklen warten. Mit dieser Strategie liessen sich verlässlich Stillstände vermeiden. Aktuellen Anforderungen an Agilität, Effizienz und Ressourcenschonung hält diese Form der Risikominimierung aber nicht mehr stand.
Problematisch ist vor allem, dass Instandhaltungsmassnahmen ungeachtet des tatsächlichen Zustands der Maschinen und Anlagen stattfinden, also auch dann, wenn gar keine Eingriffe erforderlich sind. Hier schlummert folglich nicht nur Potenzial für eine höhere Anlagenverfügbarkeit. Auch Kosten, die durch den hohen Ersatzteilbedarf sowie für die mögliche Beauftragung eines externen Wartungspartners entstehen, lassen sich deutlich minimieren.
Datenbasiert warten
Alles, was Unternehmen hierfür benötigen, sind Daten aus dem Produktionsprozess und seinem Umfeld, z. B. Drehzahlen oder Energieverbräuche. Oftmals sind diese Daten längst verfügbar und Betriebe in einer guten Ausgangsposition, um intelligente und automatisierte Wartungsstrategien zu entwickeln. Die größten Vorteile entstehen dabei durch Instandhaltungslösungen, die auf die Zustandsbewertung der eingesetzten Maschinen und Anlagen aufsetzen und sich aus verschiedenen, bewährten Ansätzen (vgl. Abbildung 1) ableiten:
- Total Productive Maintenance (TPM): Fortlaufende und ungeplante Wartung im Produktionsprozess mit Protokollierung der Aktivitäten
- Condition Based Maintenance (CBM): Von Messwerten und Zuständen abhängige unterschiedliche Wartungsmassnahmen
- Preventive Maintenance (PM): Vorbeugende (planbare) zustandsunabhängige und zyklische Wartung nach Vorschriften oder Erfahrungswerten zur Risikominimierung
- Predictive Maintenance (PdM): Vorhersagbare nicht zyklische Wartungsaktivitäten auf der Basis von Erfahrungen und Berechnungen
- Risk Based Maintenance (RBM): reine Instandsetzung nach Ausfall
- Reliability Centered Maintenance: Erreichung einer Zielverfügbarkeit durch Analyse und abgeleitete Massnahmen (Inspektion, Wartung, Reparatur)
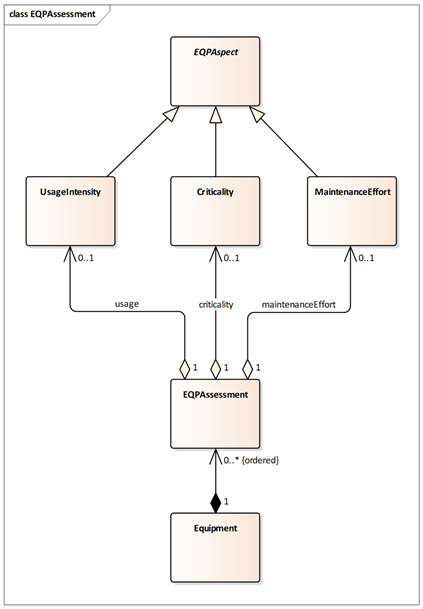
Abbildung 1: Equipment Assessment zur Festlegung der Wartungsstrategie (Quelle: PSI Automotive & Industry)
Fortlaufende Bewertung
Einmal festgelegt, sind Unternehmen gefordert, die Wirksamkeit der aus der Wartungsstrategie abgeleiteten Massnahmen fortlaufend zu überprüfen und ggf. anzupassen. Ausdrücklich gilt es hierbei auch einen zeitlichen Aspekt zu beachten. So gibt es Wartungsstrategien, die nur temporär sinnvoll sind, etwa für saisonal genutzte Anlagen, Fahrzeuge oder Ausrüstungen. Änderungen sind bspw. bei neuen Nutzungsarten erforderlich, wenn neues Equipment verfügbar ist oder durch beseitigte Engpässe vormals kritische Ressourcen als unkritisch eingestuft werden können. Einfluss auf die Wartungsstrategie haben nicht zuletzt auch Umbauten an Maschinen und Anlagen, die einer höheren Stabilität und Verfügbarkeit dienen.
Aufschlussreiche Kennzahlen
Wie gut Massnahmen greifen, lässt sich an Prozesszeiten und -kennzahlen (Key Performance Indicator, KPI) ablesen, die einen Mittelwert für die betrachtete Periode darstellen. Das heißt, die Entwicklung dieser Daten über die Zeit liefert entscheidende Hinweise auf die Wirksamkeit der durchgeführten Wartungsmaßnahmen. Auch der Erfüllungsgrad von Wartungsverträgen – sogenannte „Service Level Agreements“ (SLAs) – lässt sich auf diese Weise sicher und transparent kontrollieren. Entsprechende Vereinbarungen definieren nicht nur Zielvorgaben (Service Level Objectives, SLO) und Indikatoren (Service Level Indicators, SLI) (vgl. Abbildung 2), sie enthalten auch Vereinbarungen über Reaktionszeiten zu bestimmten Ereignissen, zur Einordnung von Incidents nach Schwere und Priorität sowie zu erwarteter Verfügbarkeit der (Software-) Systeme oder (Produktions-) Anlagen.
Abbildung 2: Prozesszeiten als Indikatoren für das Wartungsmanagement (Quelle: PSI Automotive & Industry)
Klassifizierte Prognosen
Kurzum: Ziel ist die Umsetzung einer zustandsbasierten Wartung. Hierfür können Unternehmen ihre vorhandenen Systeme mit KI-Methoden anreichern. Eine mögliche Systemarchitektur mit einem KI-basierten Modul in seinem Zentrum könnte dann wie folgt aussehen (vgl. Abbildung 3): Von einer Vielzahl numerischer und kategorischer Datenquellen aus dem Shopfloor-Bereich sowie von ERP-System, Scheduling-Lösung und MES gelangen die Eingangsdaten (Features) über entsprechende Schnittstellen in das KI-Modul. Anhand der gelieferten Daten erfolgt eine Zustandsschätzung des jeweiligen Assets und eine Vorhersageberechnung für instandhaltungsrelevante Masszahlen und Zeiten (z. B. TTF, TTR) sowie deren zeitliche Mittelwerte (z. B. MTTF, MTTF).
Darüber hinaus klassifizieren die Prognosen, wie dringlich eine Wartung durchzuführen ist. Diese Information gelangt ins
ERP-System und führt zur Auslösung eines entsprechenden Wartungsauftrags – angereichert um sämtliche Informationen, die zum konkreten Asset vorhanden sind. Das ERP-System übermittelt den Wartungsauftrag an die Scheduling-Lösung, welche die Planung übernimmt. Diese leitet den nun eingeplanten Wartungsauftrag ans
MES-System, das dessen Durchführung unter Nutzung der entsprechenden Interaktionsmöglichkeiten mit den Mitarbeitern in der Fertigung
(Werker-Assistenz) steuert. Alle integrierten Systeme – ERP-System, Scheduling-Lösung und MES – liefern ihrerseits wieder Informationen an das KI-Modul zurück.
Abbildung 3: Systemarchitektur für die Umsetzung des Anwendungsfalls „Optimierte zustandsbasierte Wartung“. Quelle: PSI Automotive & Industry
Kontinuierliche Verbesserung
Eine solche ganzheitliche Lösung bietet z. B. die PSI. So ergänzen KI-basierte Werkzeuge die integrierte
ERP-MES-Lösung, die dann als Gesamtlösung sinnvolle Wartungstermine ermittelt, steuert und umsetzt. Dreh- und Angelpunkt des KI-Moduls sind Methoden des Deep Learning und der erweiterten Fuzzy-Logik
(Deep Qualicision Technologie) sowie die Bewertung der Daten durch qualitatives Labeln.
Dies ist die Basis, um komplexe Wechselwirkungen zwischen verschiedenen Faktoren und Bedingungen identifizieren und berücksichtigen und auch unternehmerische Aspekte wie die Kritikalität einer Anlage durch unterschiedliche Gewichtung einzelner Kriterien betrachten zu können. In die Berechnungen fliessen neben den Maschinendaten auch relevante Informationen aus Aufträgen zu Materialien und Qualitätsdaten ebenso wie die Wartungshistorie und erwartete Nutzungsdaten aus bereits eingeplanten Aufträgen ein. Ist ein Auftrag abgeschlossen, gelangen die Daten ebenfalls in den Prozess und verbessern so kontinuierlich die Vorhersagen zu notwendigen Wartungsaktivitäten.
ERP + MES + KI
Der zustandsbasierten Instandhaltung gehört die Zukunft. Eine ausreichend grosse Datenbasis hierfür steht bereits zur Verfügung, ebenso wie Systeme zur Auswertung dieser Daten und ihrer komplexen Wechselwirkungen. Die Lösung: die Integration von ERP, MES und KI-Methoden zu einem durchgängigen Gesamtsystem.
Die Autoren
Karl Tröger ist Business Development Manager und seit mehr als 20 Jahren bei
PSI Automotive & Industry GmbH. In dieser Zeit hat er sich mit allen Aspekten von ERP-Software befasst und war in führenden Positionen in Entwicklung, Beratung und Marketing tätig. Heute versteht er sich als Bindeglied zwischen Kunden, Markt, Wissenschaft sowie Software-Entwicklung und Marketing. Der Diplom-Ingenieur der Elektronik und Nachrichtentechnik ist an der von der Bundesregierung initiierten Plattform Industrie 4.0 beteiligt und veröffentlicht regelmässig vielbeachtete Publikationen über die Zukunft von fertigungsnaher Software.
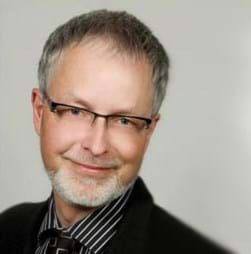
Seit mehr als 25 Jahren ist
Dr.-Ing. Thomas Müller in der Entwicklung von Software und Systemen für die Fertigungssteuerung tätig. Nach vielen Jahren in der Halbleiter- und High-Tech-Industrie entwickelt er seit 2017 für die
PSI Automotive & Industry GmbH im Rahmen der MES-Entwicklung tragfähige Visionen für die Produktion von morgen. Der Doktor der Ingenieurwissenschaften nimmt an verschiedenen Forschungsprojekten teil und beschäftigt sich mit Themen rund um Künstliche Intelligenz, Maschinelles Lernen, Leading-Edge-Technologien sowie Industrie 4.0.
Dieser Beitrag wurde ermöglicht durch PSI AG Schweiz in Wil, dem Spezialisten für ERP und MES-Software. Der direkte Austausch, ein fairer Umgang und gemeinsame Produktentwicklung sind Teil der DNA von PSI. Die Spezialisten setzen alles daran, dass ihre Kunden ihr maximales Potenzial entfalten können.
Der Beitrag erschien im topsoft Fachmagazin 22-3
Das Schweizer Fachmagazin für Digitales Business kostenlos abonnieren
Abonnieren Sie das topsoft Fachmagazin kostenlos. 4 x im Jahr in Ihrem Briefkasten.